Recognizing the Fundamentals and Applications of Plastic Extrusion in Modern Production
In the realm of contemporary production, the method of plastic extrusion plays an instrumental function. Unwinding the principles of this procedure discloses the real flexibility and possibility of plastic extrusion.
The Basics of Plastic Extrusion Process
While it might show up complex, the principles of the plastic extrusion procedure are based on reasonably uncomplicated concepts. It is a manufacturing process in which plastic is thawed and after that shaped right into a constant profile through a die. The raw plastic material, commonly in the kind of pellets, is fed right into an extruder. Inside the extruder, the plastic is subjected to heat and stress, creating it to thaw. The molten plastic is then compelled through a designed opening, referred to as a die, to form a long, constant product. The extruded item is cooled and afterwards cut to the desired size. The plastic extrusion process is thoroughly used in different markets as a result of its efficiency, adaptability, and cost-effectiveness.
Different Sorts Of Plastic Extrusion Techniques
Structure upon the standard understanding of the plastic extrusion procedure, it is necessary to discover the different strategies involved in this production technique. The 2 primary methods are profile extrusion and sheet extrusion. In account extrusion, plastic is thawed and created into a constant account, often utilized to produce pipelines, poles, rails, and home window frames. In contrast, sheet extrusion produces big, level sheets of plastic, which are generally additional processed into items such as food product packaging, shower drapes, and car parts. Each technique needs specialized machinery and exact control over temperature level and stress to ensure the plastic maintains its shape during cooling. Comprehending these strategies is key to utilizing plastic extrusion efficiently in modern-day production.

The Role of Plastic Extrusion in the Automotive Industry
A frustrating majority of components in contemporary vehicles are items of the plastic extrusion process. This procedure has revolutionized the auto market, changing it right into a more reliable, affordable, and flexible production industry. Plastic extrusion is largely utilized in the production of different automobile components such as bumpers, grills, door panels, and control panel trim. The procedure gives an uniform, consistent outcome, enabling suppliers to produce high-volume get rid of fantastic accuracy and marginal waste. The lightness of the extruded plastic components contributes to the general decrease in automobile weight, improving fuel performance. The durability and resistance of these components to warmth, cold, and effect boost the longevity of automobiles. Therefore, plastic extrusion plays a crucial role in automobile production.
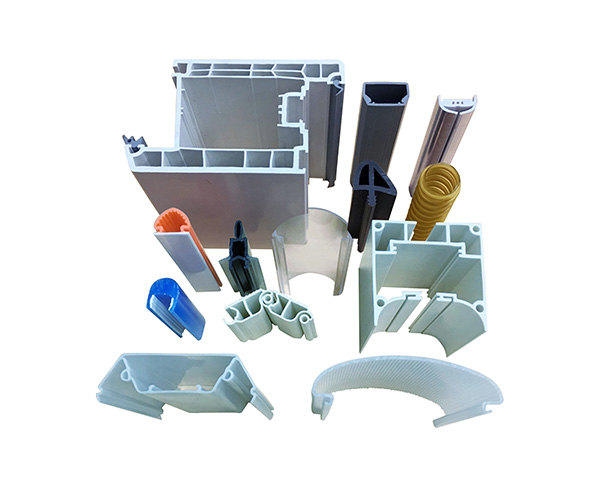
Applications of Plastic Extrusion in Durable Goods Production
Past its substantial influence on the vehicle market, plastic extrusion shows just as effective in the realm of customer items making. This process is vital in producing a broad range of products, from food product packaging to family home appliances, toys, and even medical devices. The adaptability of plastic extrusion enables manufacturers to create and create intricate forms and sizes with high precision and performance. Moreover, as a result of the recyclability of lots recommended you read of plastics, browse around these guys extruded components can be recycled, minimizing waste and cost. The versatility, adaptability, and cost-effectiveness of plastic extrusion make it a recommended option for many durable goods suppliers, adding considerably to the sector's growth and innovation. Nonetheless, the environmental effects of this widespread usage require mindful consideration, a topic to be reviewed additionally in the succeeding section.
Ecological Impact and Sustainability in Plastic Extrusion
The pervasive use plastic extrusion in making welcomes analysis of its eco-friendly implications. As a process that frequently uses non-biodegradable products, the environmental effect can be considerable. Power intake, waste manufacturing, and carbon discharges are all problems. Industry advancements are increasing sustainability. Efficient equipment reduces power usage, while waste monitoring systems reuse scrap plastic, reducing raw material demands. Additionally, the growth of eco-friendly plastics supplies an extra eco-friendly alternative. In spite of these enhancements, even more development is needed to mitigate the ecological footprint of plastic extrusion. As society leans in the direction of sustainability, suppliers have to adjust to stay practical, emphasizing the importance of continuous study and innovation you could try here in this area.
Conclusion
In verdict, plastic extrusion plays an important duty in modern-day production, particularly in the auto and durable goods industries. Its adaptability permits for the production of a variety of elements with high accuracy. Its capacity for reusing and growth of biodegradable products supplies an appealing avenue towards lasting techniques, thereby resolving ecological concerns. Recognizing the essentials of this process is key to enhancing its applications and advantages.

The plastic extrusion procedure is thoroughly used in various sectors due to its cost-effectiveness, efficiency, and flexibility.
Building upon the basic understanding of the plastic extrusion procedure, it is required to explore the various techniques entailed in this manufacturing technique. plastic extrusion. In contrast, sheet extrusion develops large, level sheets of plastic, which are normally additional refined into products such as food product packaging, shower curtains, and car parts.An overwhelming majority of components in contemporary cars are items of the plastic extrusion procedure
Comments on “Plastic extrusion for creating standardized, premium parts”